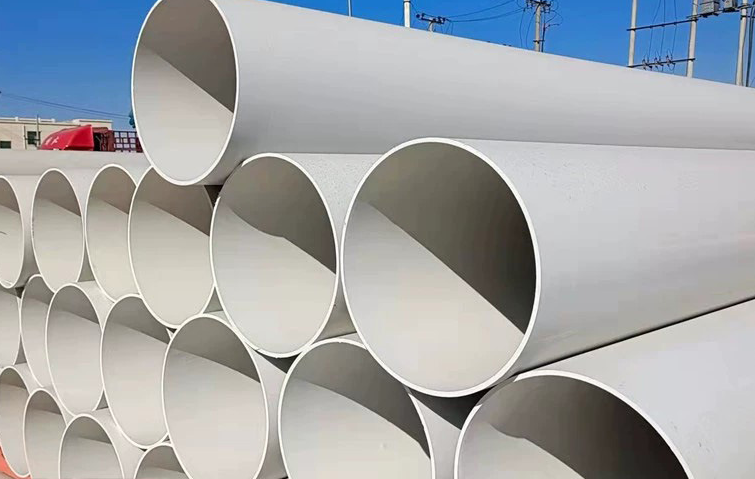
I. Processing of PVC Drainage Pipes
Extrusion Process
PVC resin, along with various additives such as stabilizers, lubricants, and pigments, is first mixed thoroughly in a high - speed mixer. The stabilizers help prevent the PVC from degrading due to heat and UV radiation during processing and its service life. Lubricants improve the flow of the material during extrusion.
The well - mixed compound is then fed into an extruder. The extruder consists of a screw that rotates inside a barrel. As the material moves through the barrel, it is heated and melted under the action of the screw's rotation and the heat provided by heating elements around the barrel. The molten PVC is then forced through a die, which shapes it into a pipe - like form. The die determines the outer diameter and wall thickness of the drainage pipe.
After extrusion, the pipe is cooled using a water bath or an air - cooling system. The cooling rate is carefully controlled to ensure the proper crystallization and mechanical properties of the PVC. A too - rapid cooling may lead to internal stresses in the pipe, while a slow cooling process may affect the production efficiency.
Cutting and Length Adjustment
Once the pipe is cooled and solidified, it is cut to the desired length. This can be done using a saw - type cutter or a flying saw, which can cut the continuously extruded pipe into individual segments without stopping the extrusion process. The length of the pipe segments is usually adjusted according to customer requirements, such as for residential drainage systems, where shorter lengths may be more suitable for easy installation in confined spaces, or for industrial applications, longer lengths may be preferred to reduce the number of joints.
II. Customization of PVC Drainage Pipes
Color Customization
In addition to the common white color, PVC drainage pipes can be customized into other colors. For example, in some building projects, pipes may be colored to match the overall color scheme of the building's exterior or interior. The color is added to the PVC compound during the mixing stage by adding pigments. Different pigments can provide a wide range of colors, from light pastels to darker shades.
For pipes used in outdoor applications, UV - resistant pigments are often added to prevent the color from fading due to sun exposure. This is especially important for pipes that are visible and need to maintain their aesthetic appearance over time.
Size and Shape Customization
The diameter of PVC drainage pipes can be customized according to specific drainage requirements. For small - scale domestic drainage, pipes with diameters ranging from 50mm to 110mm are commonly used. However, for large - scale industrial or municipal sewage systems, pipes with diameters of several hundred millimeters or even larger can be produced. The shape of the pipe can also be customized in some cases. For example, corrugated PVC pipes can be manufactured to provide better flexibility and impact resistance, which are suitable for applications where the pipe may need to withstand ground movement or external pressure.
Connection and Fitting Customization
PVC drainage pipes can be customized with different types of connections. There are socket - and - spigot joints, where one end of the pipe (the spigot) fits into the socket of another pipe. Glue or rubber seals are often used to ensure a watertight connection. Threaded connections can also be used, especially for pipes that need to be connected to other equipment such as pumps or valves. Custom - made fittings such as elbows, tees, and reducers are also available to allow for complex drainage system layouts. These fittings are usually injection - molded and designed to have the same material and performance characteristics as the pipes.
III. Processing of White Plastic Drainage Pipes (Assuming They are Also PVC - based)
The processing of white plastic drainage pipes (if they are PVC) is similar to the general PVC drainage pipe processing described above. The white color is usually achieved by adding titanium dioxide (TiO2) as a pigment during the mixing stage. TiO2 provides a bright white color and also has some UV - protection properties, which helps maintain the color and integrity of the pipe over time. The extrusion, cooling, and cutting processes follow the same principles as for regular PVC drainage pipes.
IV. Processing of Large - Diameter Sewage Pipes
Extrusion Challenges and Solutions
For large - diameter sewage pipes, the extrusion process requires more powerful extruders. The screw diameter and length - to - diameter ratio of the extruder need to be adjusted to handle the large volume of material required for the thick - walled, large - diameter pipes. The die design is also more complex, as it needs to ensure the uniform distribution of the molten PVC around the large circumference to form a pipe with a consistent wall thickness.
To support the heavy weight of the extruded large - diameter pipe during cooling, special cooling beds are used. These cooling beds may have rollers or other support mechanisms to prevent the pipe from sagging or deforming due to its own weight.
Reinforcement Techniques
Quality Control for Large - Diameter Pipes
Quality control for large - diameter sewage pipes is more critical due to their importance in sewage transportation systems. Non - destructive testing methods such as ultrasonic testing and visual inspection are used to check for internal defects such as voids and cracks, as well as external surface imperfections. The wall thickness is also carefully measured at multiple points along the pipe's length to ensure it meets the specified design requirements.
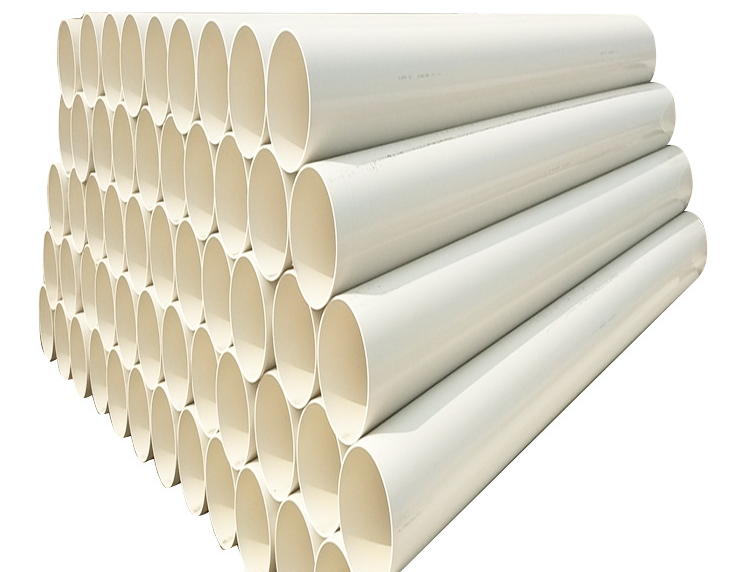